Pulsed Laser Deposition (PLD) - Introduction
LASER (Light Amplification by Stimulated Emission of Radiation) was first
demonstrated in 1960. Since then it has been developed into a powerful tool in many
application. It is especially useful in material processing [1]. Laser possesses many unique properties
such as narrow frequency bandwidth, coherence and high power density. Often the light beam is intense
enough to vaporize the hardest and most heat resistant materials. Besides, due to its high precision,
reliability and spatial resolution, it is widely used in the industry for machining of thin films,
modification of materials, material surface heat treatment, welding and micro patterning. Apart from these,
polycomponent materials can be ablated and deposited onto substrates to form stoichiometric thin films.
This last mentioned application of LASER is the so-called pulsed laser deposition (PLD) [2].
In general, the idea of PLD is simple. A pulsed laser beam is focused onto the surface of a solid target.
The strong absorption of the electromagnetic radiation by the solid surface leads to rapid evaporation of
the target materials. The evaporated materials consist of highly excited and ionized species.
They presented themselves as a glowing plasma plume immediately in front of the target surface if the ablation
is carried out in vacuum. The figure underneath shows some typical plasma plumes produced during PLD process.
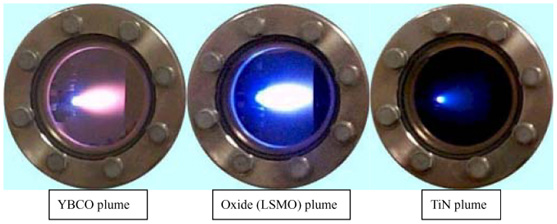
Plasma Plumes of different materials
Indeed, PLD is so straightforward that only a few parameters, such as laser energy density and pulse repetition rate,
need to be controlled during the process. The targets used in PLD are small compared with the large size required
for other sputtering techniques. It is quite easy to produce multi-layered films of different materials by sequential
ablation of assorted targets. Besides, by controlling the number of pulses, a fine control of film thickness down to
atomic monolayer can be achieved. The most important feature of PLD is that the stoichiometry of the target can be
retained in the deposited films. This is the result of the extremely high heating rate of the target surface ( K/s)
due to pulsed laser irradiation. It leads to the congruent evaporation of the target irrespective of the evaporating
point of the constituent elements or compounds of the target. And because of the high heating rate of ablated
materials, laser deposition of crystalline film demands a much lower substrate temperature than other film growth
techniques. For this reason the semiconductor and the underlying integrated circuit can refrain from thermal
degradation.
In spite of the said advantages of PLD, some shortcomings have been identified in using this deposition technique.
One of the major problems is the splashing or the particulates deposition on the films. The physical mechanisms
leading to splashing include the sub-surface boiling, expulsion of the liquid layer by shock wave recoil pressure and
exfoliation. The size of particulates may be as large as a few micrometers. Such particulates will greatly affect the
growth of the subsequent layers as well as the electrical properties of the films. Another problem of PLD is the
narrow angular distribution of the ablated species, which is generated by the adiabatic expansion of laser, produced
plasma plume and the pitting on the target surface. These features limit the usefulness of PLD in producing large
area uniform thin films, and PLD has not been fully deployed in industry. Recently remedial measures have been
proposed. Inserting a shadow mask is effective to block off the large particulates. Rotating both the target and
substrate can help to produce larger uniform films.
References:
- S.M. Metev and V.P. Veiko, Laser Assisted Microtechnology, Springer, Berlin, Heidelberg (1994)
- D.B. Chrisey and G.K. Hubler, Pulsed Laser Deposition of Thin Film, John Wiley & Sons, Inc., New York (1994)
>